Part Redesigns (Bracket)
Improving the current manufacturing process
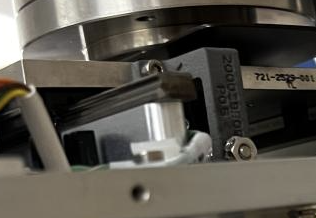
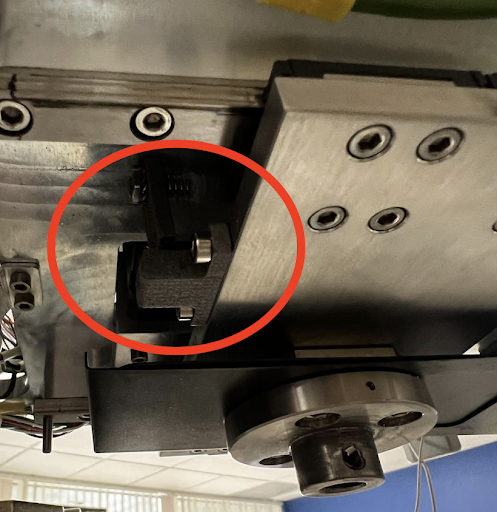
Alcon's transition into 3D plastic printing has overall been a very successful process, saving them time, money, and lowering their environmental impact. However, there have been issues with some of the plastic printed parts. These parts break during assembly and transportation of the surgical device. Part redesigns can potentially improve their current manufacturing process by reinforcing these parts to withstand necessary stresses.
Bracket Redesigns
A microscope headpiece that weighs approximately 25 pounds is supported using two identical L shaped brackets. These brackets were originally aluminum, but were subsequently produced using 3D printed Nylon 12 without any additional redesigning. The bracket performs as intended in cycle testing, but fails in assembly and transportation due to additional external forces.
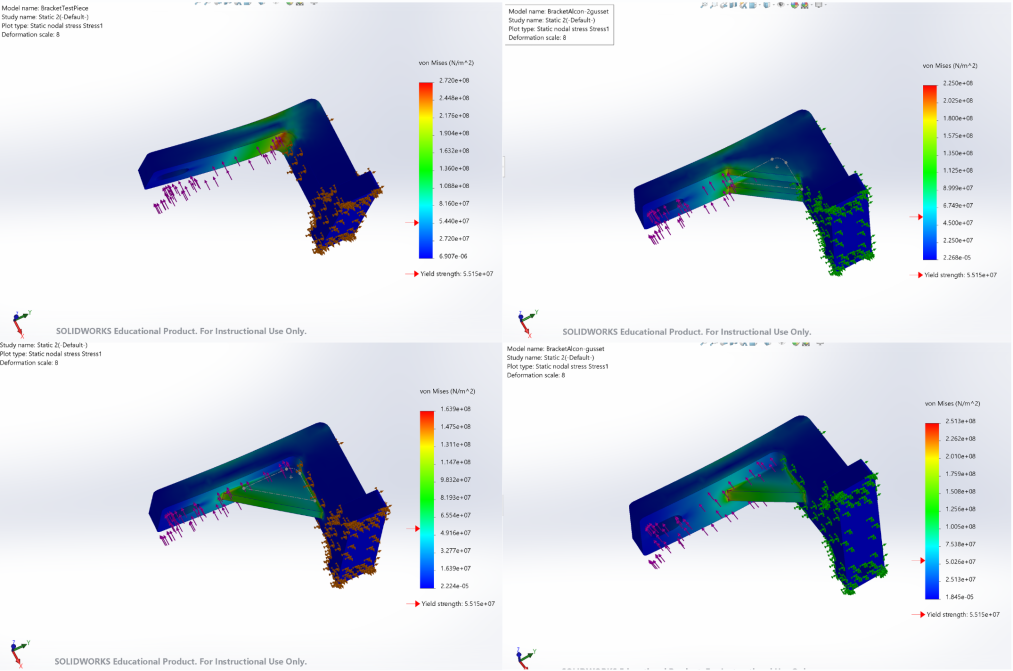
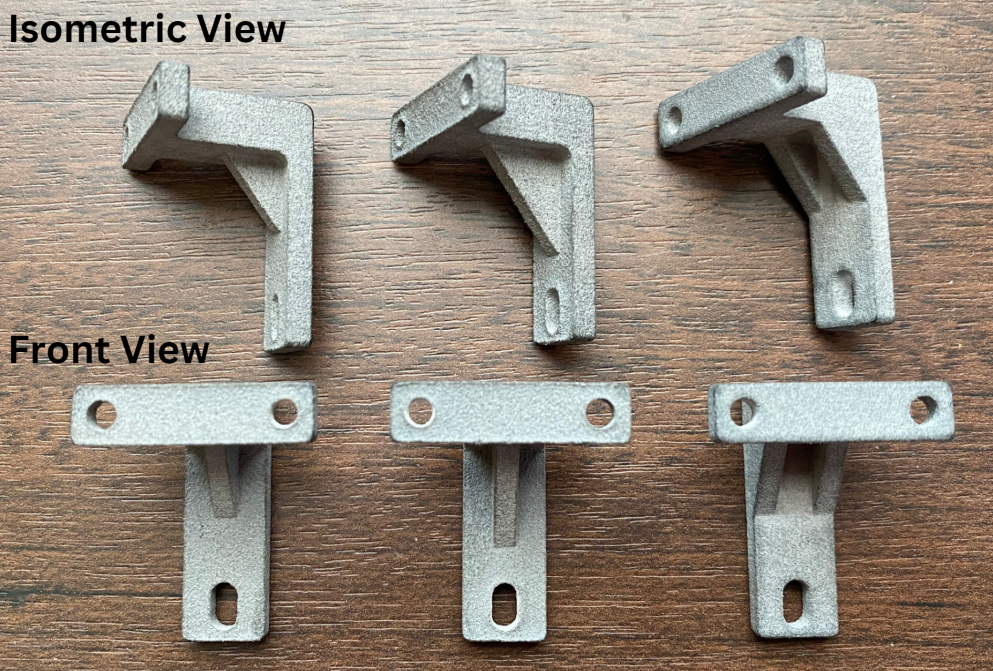
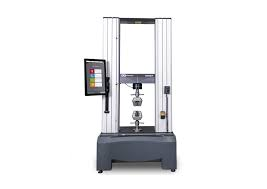
The stress simulation is used to isolate the failure point so that we can address this issue. Our design criteria for the bracket includes complying with the constraining dimensions of the assembly. We aim to optimize the part to have the smallest total volume while still meeting our acceptance criteria. Our acceptance criteria is that the bracket should withstand at least 40 pounds of applied force in compression, tension, and torsion testing using an Instron.